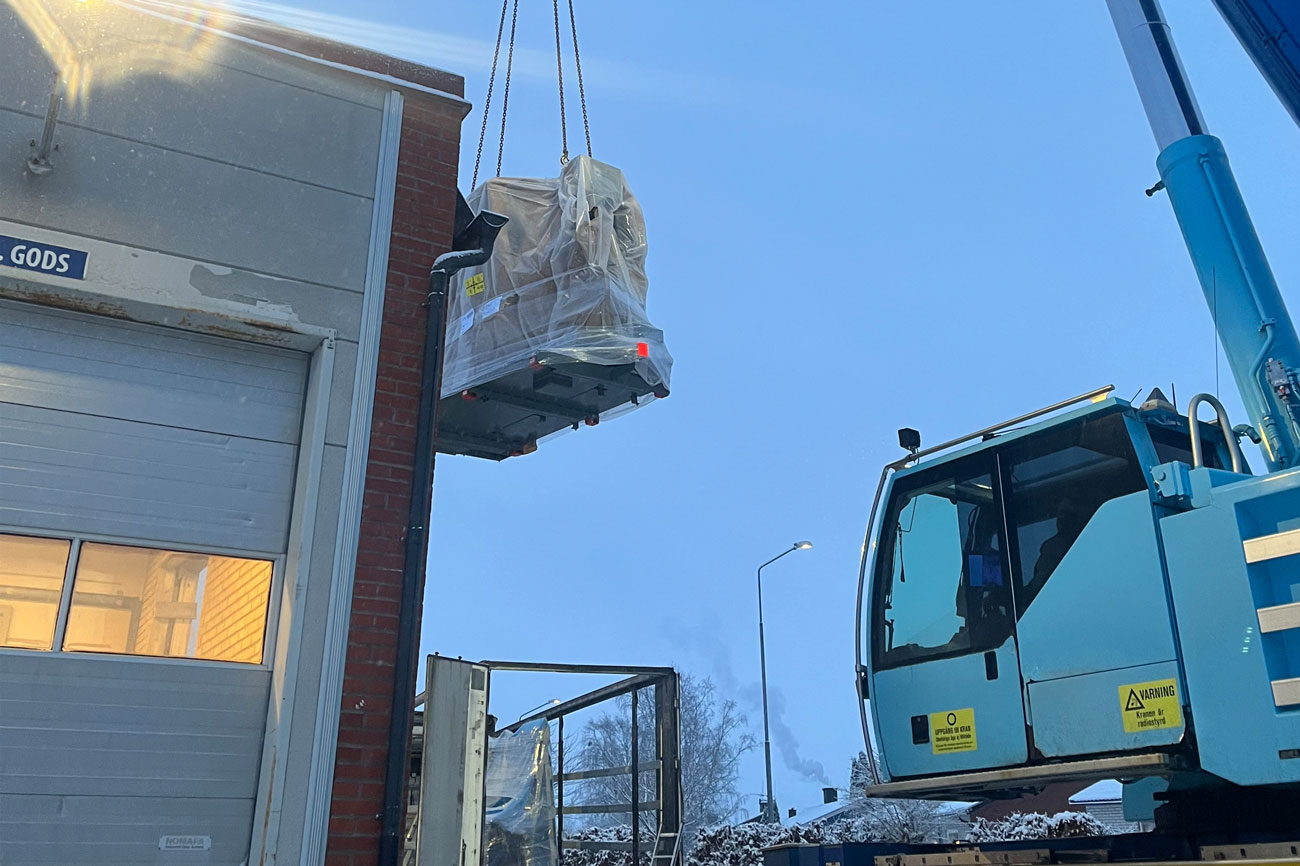
Shit! The new machine is too big!
EWES's maintenance manager, Peter Josefsson, had to scratch his head both once and twice when the NC machine from Bihler was to be installed.
Peter, three quick ones!
- How long have you worked at EWES?
About nine years - What do you do at EWES?
I work as a maintenance manager, so I manage the ongoing maintenance of both machinery and property. I am also responsible for the tools department. - Which is your favorite spring and why?
I don't have a particular favorite, instead I want to highlight my fantastic colleagues. They have an enormous knowledge of spring manufacturing and I have probably never encountered a problem that one of them couldn't help me with.
Conclusion:
Although the EWES' machinery is fantastic, it is still the employees who make the difference
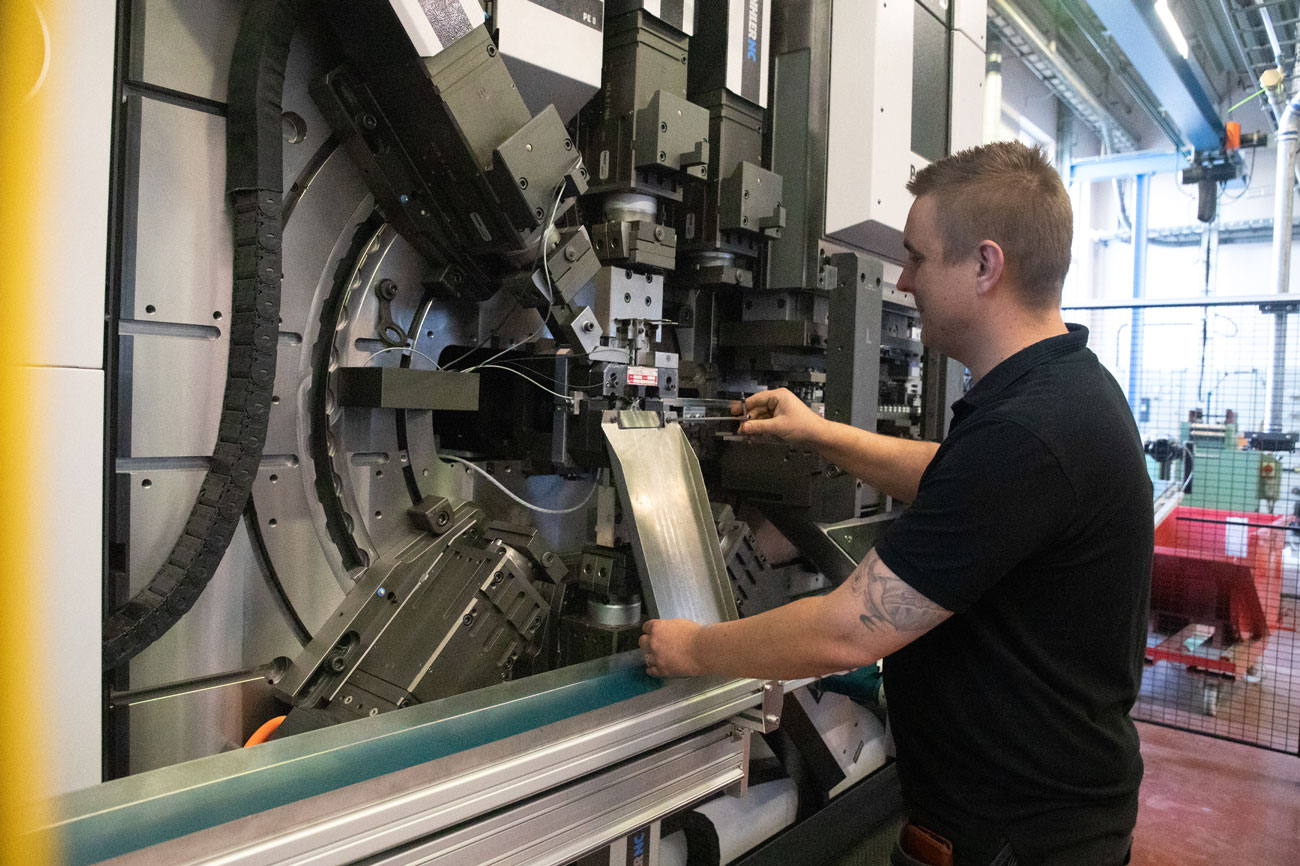
Before we tell you more about the challenges of getting the Bihler machine in place and what benefits it gives you as a customer, let us first briefly report on the investment in the press department.
In a previous article, we talked about the major investment taking place at the EWES press department. The layout has been redesigned to create a better workflow. A new press hall has been prepared to accommodate all the new investments. Tool maintenance, which previously worked in the basement, has moved into the press hall, which provides a super-fast and flexible tool movement during maintenance work.
The aim of the rebuilding has been to give the customers (and ourselves) one of Northern Europe's most modern machine parks. One of the cogs in this investment is the hyper-fast NC machine, Bihler Grm-Nc, which at the time of writing is only available in a handful of copies in the Nordics. In the press hall, you will also find three automatic presses with 25, 50 and 125 tons of press power as well as four mechanical multi-slide presses. All machines will be operated by a few Bihler-trained employees, and the ambition is for the machines to be able to produce 24/7.
Back to machine installation
When the 11-ton machine was to be installed, it was not entirely without problems. Peter Josefsson, maintenance manager at EWES says that the ceiling height contributed to that.
“It was not easy to get the machine in house because the ceiling height was too low in several places within the factory. We had to tear down one of the inner walls and dig a bigger hole in the outer wall to get the machine in. When we then had to move the machine, the challenge was that the floor area partially extended over a basement level. The machine weighs 11 tons so there was some concern about the floor giving way, so we were careful to properly brace the basement ceiling. However, the whole move went well and just a day or so later, Bihler's technician was on site to start up the machine.”
Can you describe the benefits of the machine that put EWES on the map?
“The machine is a servo-controlled multi-slide press. This means that we can shape a detail from several different directions. This in turn means that we can produce very complicated details at high speed while using the material to the maximum. Since we are able to optimize production in real time, we can see how much of the machine's capacity is actually being used and where there is time to save. For the customer, this means that we have extremely short setup times and that we can produce at twice the speed, sometimes more.”
Extremely short setup times you say - how is that possible?
- Much of the explanation for the short setup times lies in the tool changes. If we compare the old machines with the new, the tool changes are almost like comparing night and day. In the old machine, it was very labour-intensive and time-consuming work. The entire machine also had to be reset manually afterwards. In the new NC machine, all this work is automated and can more or less be carried out with the push of a button. We will also be able to use Bihler's LEANTOOL concept with standardized tool parts, which allows us to offer our customers significantly cheaper tools, up to 70 percent in fact.